Three pillars of our efforts to enhance quality
We strive to continue to offer customers the KAMEDA SEIKA taste they have long loved, and to maintain our reputation for trustworthiness by continuing to meet consumer expectations regarding safety and reliability. Accordingly, our various departments have come together to create our three-pillar approach and are focusing their energy on enhancing quality at every step of the process; from the procurement of ingredients to the development and production of products, and even to the extent of collecting customer opinions and requests and feeding this information back into the Company. Here we speak to some of the leaders who are driving these initiatives within their workplaces.
Customer Service Office perspective
Listening to customer feedback and turning it into the starting point for better manufacturing
Masanobu Kawaguchi, Head of the Customer Service Office
Each day, the Customer Service Office receives around 60 to 70 messages from customers via phone and email. After carefully listening to each one, we proceed to digitally record all opinions and requests related to concerns over safety, reliability, or taste, and then make daily, weekly, and monthly reports to all relevant departments. We also present customer feedback directly to executives at the Management Meeting.
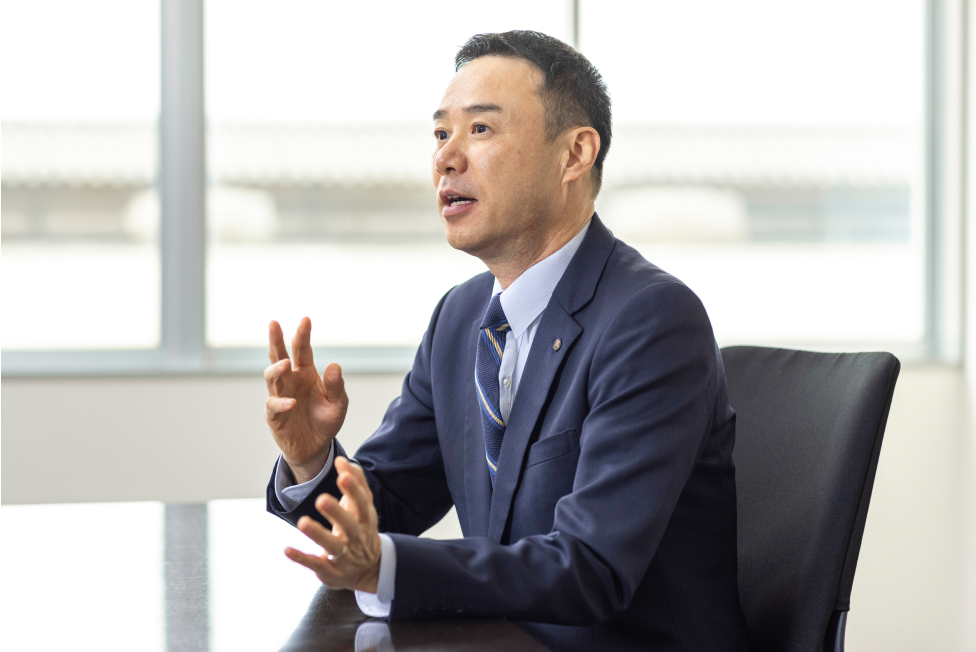
Responding earnestly to all customer feedback
Responding to all feedback, even feedback that some might consider to be trivial, is the first step toward improvement and change. Our vital role is to share this feedback with our factories and the Purchasing Department.
Previously, we heard from a customer who was anxious about the quality preservation agent that we insert into all package of our product Happy Turn, our long-selling product. Since each Happy Turn cracker is wrapped individually, this customer was concerned that the preservation agent might accidentally be wrapped up along with the individually wrapped crackers. Of course, even if this were to happen it would not damage the customer’s health, but we recognized that this was an issue that we had the ability to address in order to alleviate the concerns of customers, who demand safety and reliability. So we shared this customer feedback with our factories and the Purchasing Department, and introduced packaging that used new materials which allowed us to maintain Happy Turn’s distinctive crisp texture without using those quality preservation agents.
Aligning with our customers on health and environmental issues
In recent years, we have received an increasing number of customer opinions regarding the reduction of our plastic usage, as well as inquiries on health-related topics such as allergens, sodium levels, and sugar content. We understand through this feedback that our customers are becoming increasingly aware of environmental issues and health. By further analyzing these trends and collaborating with other departments, we hope to accelerate further initiatives that are relevant to our customers.
In order to apply customer feedback to enhance our product quality, we must have a feeling of being close to our customers. We will continue to work to strengthen our three-pillar, collaborative approach so that our customer feedback can be tied into not only our product quality, but also into improving the environment that surrounds our products.
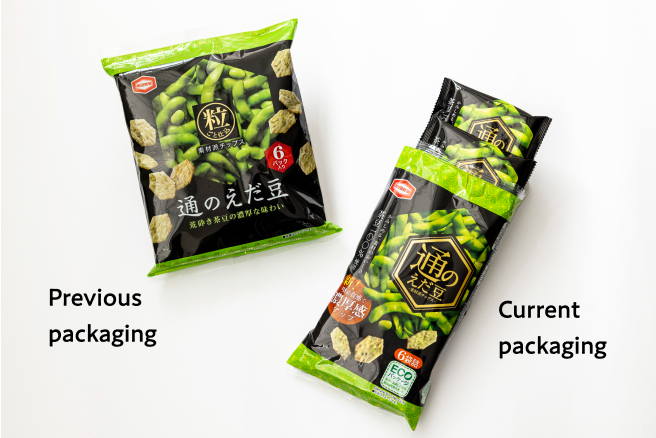
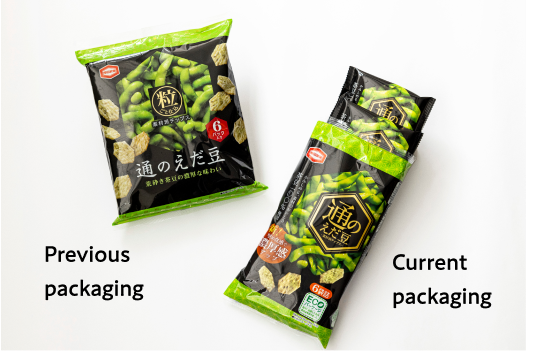
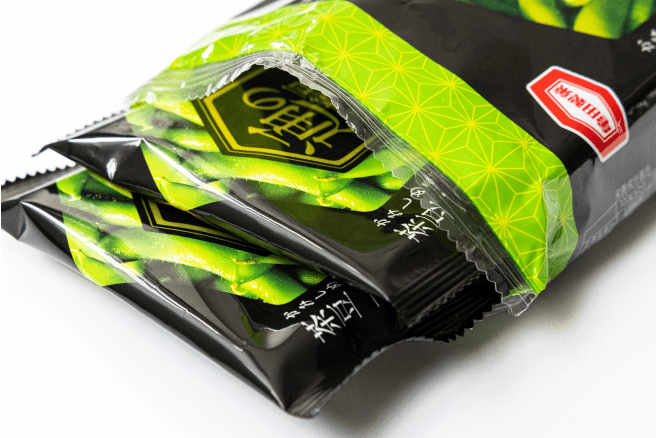
In response to increasing customer awareness of the environment, we changed some of our product packaging to be slimmer. We removed the trays used to separate crackers, and changed the exterior bag to fit the inner bags perfectly, reducing the amount of plastic used by 30%. Packaging like this has an ECO-package mark.
Purchasing Department perspective
Becoming even more “Better For You,” by procuring better ingredients
Kazutaka Nishiyama, General Manager of the Purchasing Department
It is the Purchasing Department’s responsibility to procure everything that is needed to produce our products—from food ingredients to packaging materials—and supply it to our factories. With a focus on safety, reliability, and excellent flavor, we are very selective about our business partners and carry out business negotiations so that we can stably and continuously procure ingredients and materials that always meet the same high standards. To ensure that we are able to hold discussions with highly specialized partners as equals, our department includes several individuals with experience of product development and manufacturing.
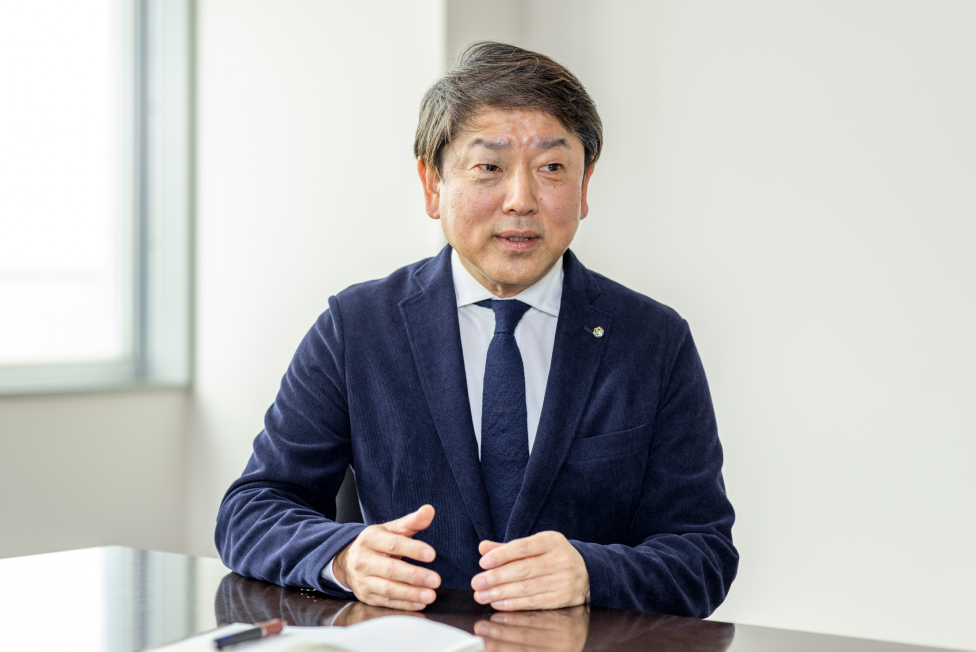
Factory and customer requests reflected in our ingredient procurement strategy
We procure various types of rice, the primary ingredient used in our rice crackers, from production areas throughout Japan. At our factories, we use ingredients – which may differ in terms of water content, amylose content, etc. – in a way that is optimized for each type of rice cracker. That is why we very carefully consider the characteristics of each type of rice that we procure, such considering certain rice that is ideal for soft rice crackers, and certain rice that is ideal for hard rice crackers. However, we still sometimes have ingredients rejected by factory managers, who tell us that the ingredients do not meet the quality level they require. That is why we always endeavor to maintain direct communications with the factories while we work.
Aiming for sustainable ingredient procurement under our three-pillar approach
In recent years, global warming and other changes have significantly affected the optimal areas for food production, making sustainable procurement a major issue. Other important issues include the use of non-fossil fuels and a reduction in plastic usage. We take into account every bit of information that is shared with us by the Customer Service Office, and we put all of it to practical use in our procurement of ingredients. Recently, much of the customer feedback we receive has included guidance or opinions related to SDGs. This has been indispensable information that will assist us in our pursuit of materials that cater to modern needs.
We recognize that we must work toward environmentally-aware manufacturing under our three-pillar approach, where we all bring knowledge to the table from our varying perspectives of ingredient procurement, customer service, and production.
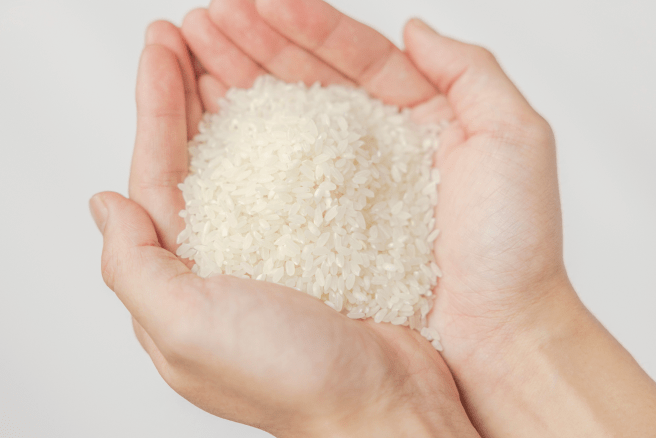
Rice is sourced from all over Japan, with varieties matched to each type of rice cracker. Working with our factories, we are in constant pursuit of better quality.
Production Division perspective
Maintaining KAMEDA SEIKA taste with collaborative strengths that create excellent products
Tatsuya Ishimoto, Head of Shirone Plant
To maintain our unchanging delicious taste, we implement thorough quality control for every process at our factory, from receiving ingredients to preparing them, creating the products, seasoning, and packaging. After the final product is completed, dedicated quality staff carry out stringent checks. We do not miss even tiny discrepancies in taste, smell, or texture. Safety and quality are ensured by both high-precision machinery and human senses and techniques. Factories are the places where we create products that exceed our customers’ expectations.
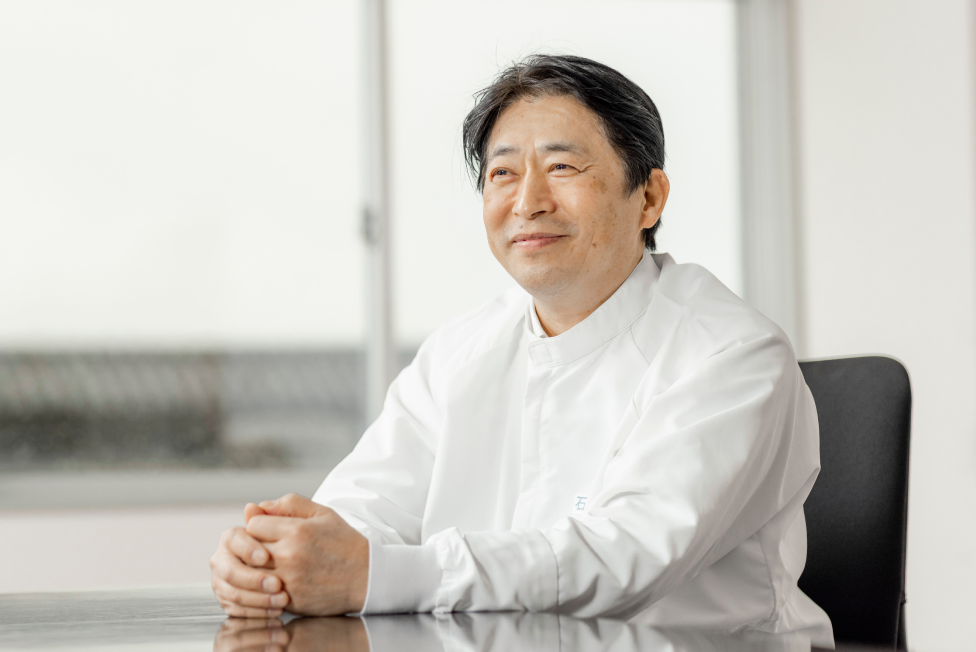
Transparency and ease of communication with the Purchasing Department
The key to making delicious rice crackers comes from the process of steaming rice flour and forming it into a dough. Considering this, the quality of the rice that we use is of paramount importance. The time of the year when we are especially nervous is during the new rice harvest. Although freshly-harvested rice is delicious when cooked and eaten as is, it can actually present a variety of problems when it comes to making it into a dough. That is why we work very closely with the Purchasing Department to receive new rice every year as soon as possible in order to carry out tests at our factories to set the specific conditions for the year’s rice. The Purchasing Department also implements strategies such as holding new rice for a while before supplying it to the factories.
This attention to quality does not stop at rice though; we depend on quality for all of our ingredients. If we cannot maintain a strong relationship between our factories and the Purchasing Department, where needs and dissatisfaction can be communicated without hesitation, we would not be able to make good products.
Improvements to KAMEDA Kaki-no-Tane via three-pillar approach
At our weekly collaboration meetings, we deliberate any problems that may have arisen during factory sample tests and whether or not there are changes to the ingredients the Purchasing Department has procured. The meetings also provide a venue to discuss solutions to customer opinions shared by the Customer Service Office.
For example, customer feedback indicating a desire for lighter and crisper KAMEDA Kaki-no-Tane became the starting point to an improvement initiative that we decided to undertake. A lighter texture and a fragile product are two sides of the same coin though, so therefore, the Purchasing Department had to undertake a review of ingredient selection. We included the rice flour manufacturer in the development process, which allowed us to reformulate the product into an even better version of KAMEDA Kaki-no-Tane.
Going forward, we will continue to place value on this relationship that enables us to cooperate in real-time, and will work to use this three-pillar approach to develop new products and improve quality.
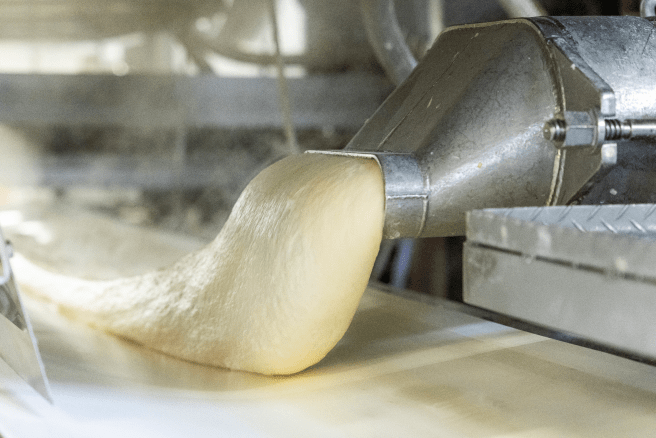
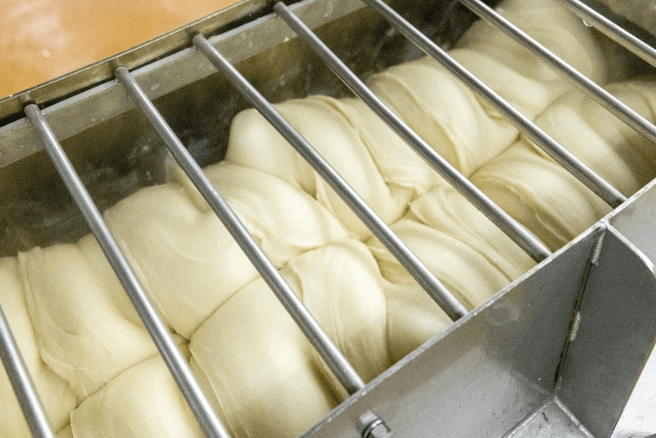
Rice flour is steamed and formed into a dough, a process that is key to rice crackers’ delicious taste. As the characteristics of the rice may necessitate adjustments to the equipment, collaboration with the Purchasing Department in advance is vital.
*Departments, positions, and duties are those as of the time of each interview.